Mold Making Guide
A Primer on Silicone RTV
RTV stands for "Room Temperature Vulcanizing". This means that the silicone will cure at room temperature, without the need of expensive oven heating. However, the higher the ambient temperature, the quicker RTV cures.
There are two basic types of silicone mold making products available. They are Polycondensation or Tin Cure and Polyaddition or Platinum Cure.
The Polyaddition/Platinum Cure is the most expensive of the two. It offers better mold stability and less shrinkage. However it is susceptible to inhibition from a wide variety of materials, and must be handled very precisely to produce a good cure.
Polycondensation/Tin Cure silicone is less expensive, has a virtually trouble-free cure, and is not sensitive to inhibition. This is the kind of silicone in TAP Silicone RTV System.
On the following pages you will see instructions using the Rhodorsil RTV2. Please note that even though the name is different, the instruction also applies to TAP Silicones. We hope you find these pages helpful in your mold making journey.
TAP Silicone RTV System for Imprint and Reproduction
TAP Silicone RTV's are used in molding are two-component, room temperature curing elastomers.
TAP Silicone RTV's silicone elastormers have specific properties which provide users with many advantages;
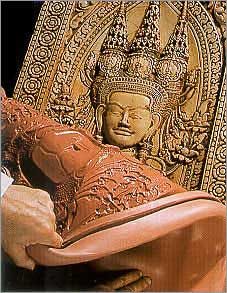
Flexibility
Easy to demold
Fine reproduction detail
High tear strength
Room temperature curing, no heat release
Easy to use, without any heavy equipment
Aging resistance
Heat stability
Dielectric properties
Low shrinkage
There are 2 different types of RTV2;
1. Polycondensation RTV2 (PC)
2. Polyaddition RTV2 (PA)
Polycondensation type TAP Silicone RTV System is supplied as base and catalyst, polyaddition type TAP Platinum Silicone is supplied as Part A and Part B.
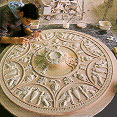
Each of these types have specific features that means it must be chosen according to the user's requirements.
Curing starts once the two components are mixed at a rate that depends on the operating conditions. The ideal conditions are; 23°C ambient temperature, 50% relative humidity
In order to comply with dimensions it is preferable to use; moderate temp. 23 - 30°C and in any case no less than 20°C minimum 30% humidity comply with the recommended catalyst dosage
SILICONE RTV Application
There are numerous molding applications for SILICONE RTV's, a few of them are mentioned below.
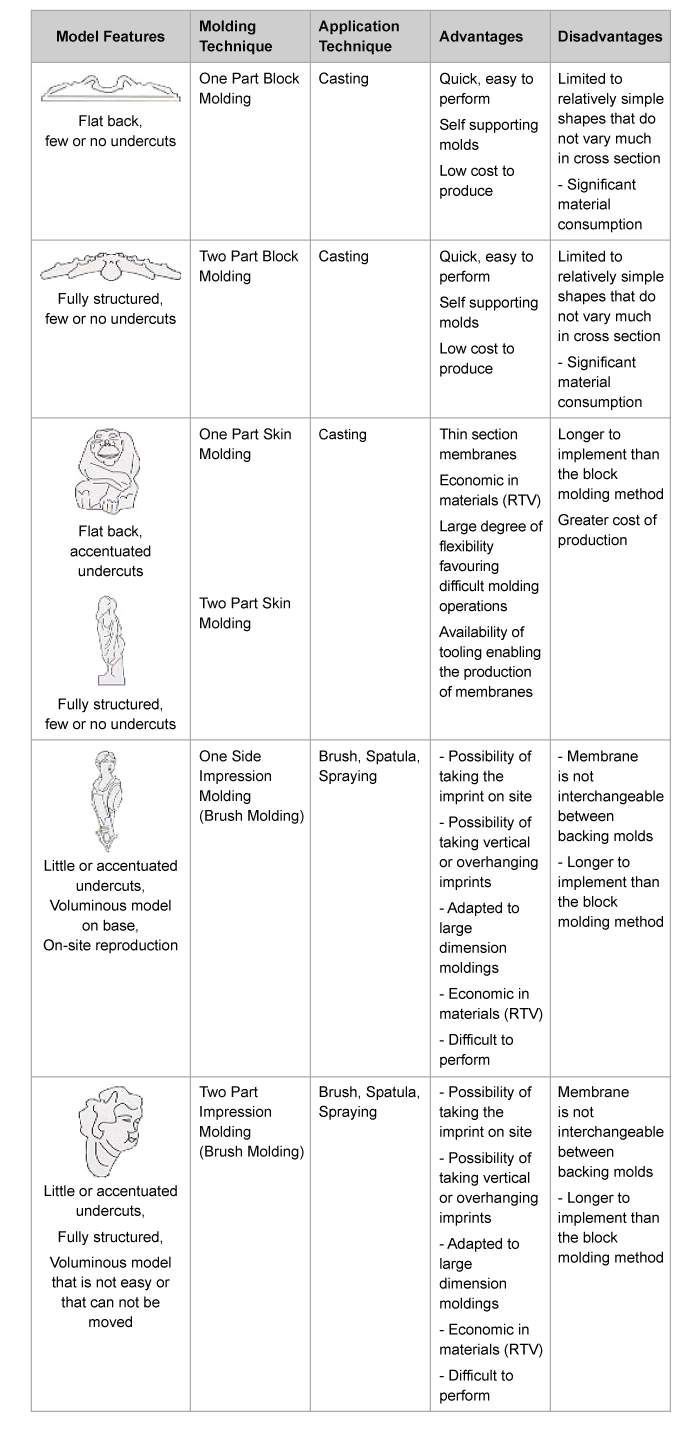
Preparing the Mold
Models are made in a wide range of materials whose surface conditions and porosity differ. Even though SILICONE RTV does not adhere to most materials, it is usual to take certain precautions before taking impressions. Various possibilities are offered below which are tested in laboratories.
Moulding Techniques
SILICONE RTV enable moulds to be made for all types of applications using a few basic principles. In spite of the multiple variants that are possible, basic processes exist which are described below.
Two Part Block Molding
One Part Skin Molding
Two Part Skin Molding
One Side Impression Molding (Brush Molding)
Two Part Impression Molding (Brush Molding)
Advice to Users
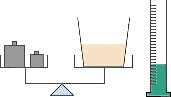
Mix the two components in the recommended proportions.
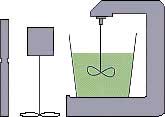
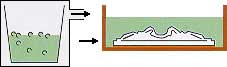
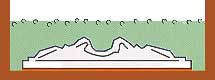
The catalysed mixture is degased under a vacuum of 20-50 mbar. The RTV will expand under the action of the vacuum and it is therefore necessary to have a container of appropriate size. Degassing is not required for TAP Platinum Silicone. It's low viscosity provides easy bubble release.
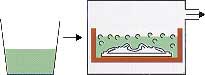
However, prolonged degasing can cause loss of certain components that are required for curing.